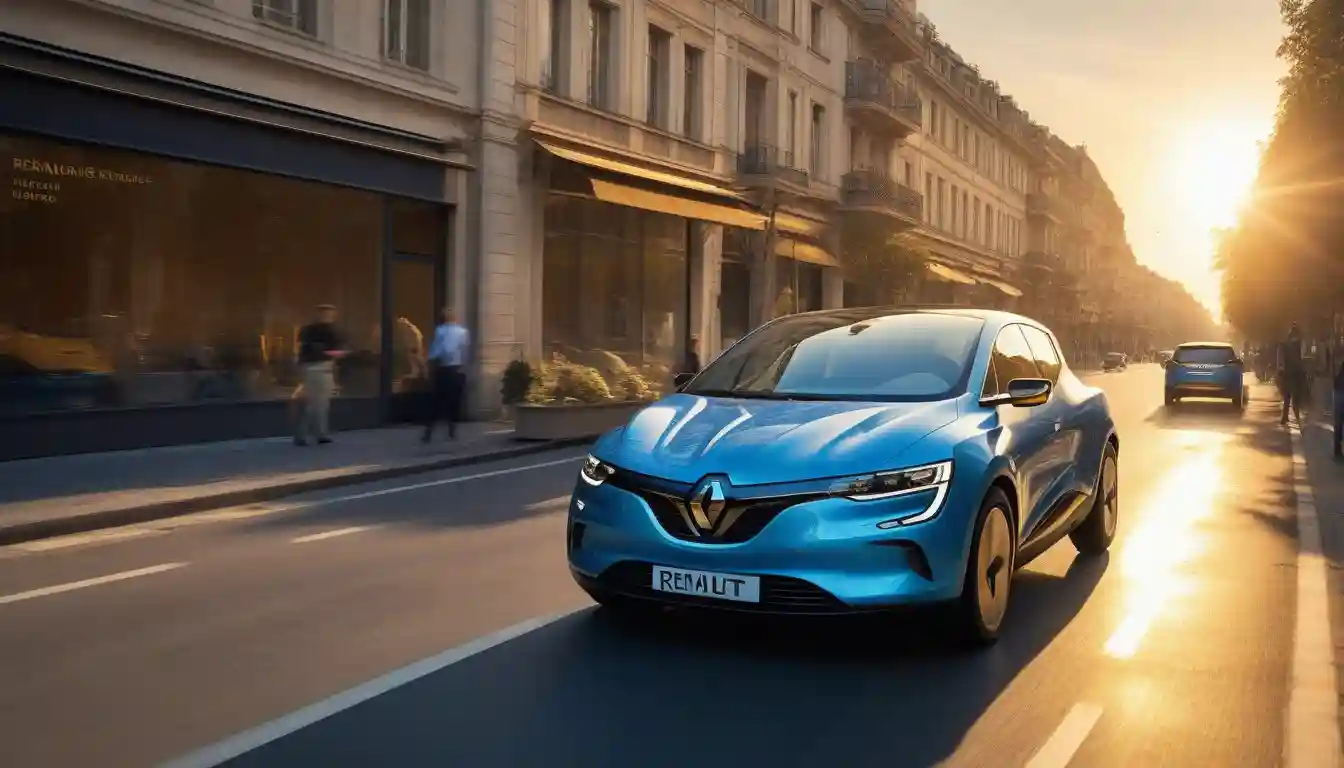
Renault's Strategic Move: 20% Battery Cost Reduction Plan
Renault's Plan to Cut Electric Vehicle Battery Costs by 20%
Renault SA has revealed its intention to reduce battery expenses by around 20% through the adoption of a new, more economical cell chemistry and an innovative production process for its electric vehicles (EVs). The French automaker's Ampere unit is set to incorporate lithium iron phosphate (LFP) cells alongside the existing nickel cobalt manganese (NCM) process, as per a statement released on Monday. This strategic move is part of a collaboration with China's Contemporary Amperex Technology Co. and South Korea's LG Energy Solution.
The integration of LFP cells and the implementation of a new cell-to-pack technology aim to lower battery costs in Renault's vehicles starting from 2026. These changes will also facilitate a greater number of cells to be packed into a given space, thereby improving efficiency. Renault and its partners are concentrated on establishing a robust "value chain" in Europe, where the production will be based.
This transition to LFP chemistry aligns with the wider industry trend of migrating away from more expensive NCM batteries. By persisting in producing both battery types, Ampere aims to remain competitive despite facing challenges from lower-priced Chinese models, even in light of new EU tariffs aimed at hindering their market penetration.
Key Takeaways
- Renault is planning to reduce battery costs by 20% through the adoption of cheaper cell chemistry.
- Ampere is set to integrate lithium iron phosphate (LFP) cells into its EV platform.
- Collaboration with CATL and LG Energy Solution will focus on implementing new cell-to-pack technology.
- The reduction in battery costs is expected to commence in early 2026, with production taking place in Europe.
- Renault intends to continue producing both LFP and NCM battery types.
Analysis
Renault's decision to embrace LFP cells and new production technology has the potential to disrupt the EV battery market, benefiting CATL and LG Energy Solution. This shift decreases reliance on NCM, impacting suppliers such as Panasonic. Economically, the reduction in battery costs may contribute to an increase in Renault's sales and the adoption of EVs in Europe. Politically, it serves as a response to EU tariffs on Chinese EVs. In the long run, Renault's dual-battery strategy enhances market adaptability, which is crucial as battery technology evolves.
Did You Know?
- Lithium Iron Phosphate (LFP) Cells:
- LFP cells are a type of lithium-ion battery that utilizes lithium iron phosphate as the cathode material, in contrast to the more prevalent nickel cobalt manganese (NCM) cathodes.
- They are recognized for their stability, long cycle life, and safety, albeit generally having lower energy density compared to NCM batteries.
- LFP batteries are typically more cost-effective to produce and are less susceptible to overheating, making them a preferred choice for applications with cost sensitivity and regions with less stringent energy density requirements.
- Cell-to-Pack (CTP) Technology:
- Cell-to-pack technology represents an advanced method of battery assembly that eliminates the necessity for individual battery modules, directly integrating cells into a battery pack.
- This approach reduces the complexity and weight of the battery system, resulting in cost savings and increased energy density.
- CTP technology allows for more efficient utilization of space within the battery pack, enabling the inclusion of more cells and enhancing the overall energy storage capacity of the vehicle.
- Value Chain in Battery Production:
- The term "value chain" in the context of battery production encompasses the entire process from raw material extraction to the manufacturing of battery cells and packs, and ultimately their integration into electric vehicles.
- Establishing a robust value chain involves ensuring a reliable and cost-effective supply of materials, efficient production processes, and a strong distribution network.
- For Renault, emphasizing a value chain in Europe entails controlling and optimizing each step of the battery production process within the region, potentially reducing reliance on external suppliers and mitigating risks associated with global supply chain disruptions.