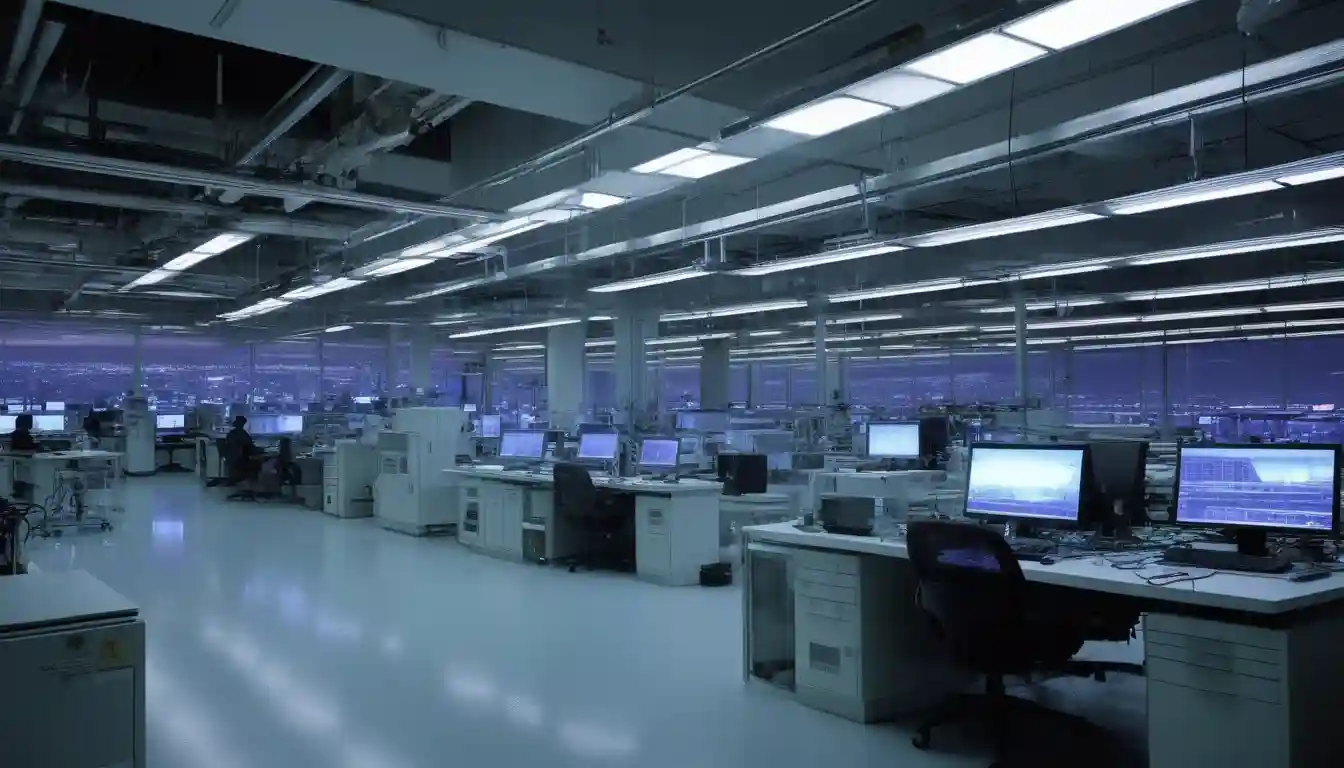
Samsung Becomes First in Korea to Adopt 64-Hour Workweek for Chip R&D as It Races to Regain Semiconductor Edge
Samsung’s 64-Hour Workweek Experiment: High-Stakes Acceleration in a Race for Semiconductor Supremacy
In the Global Chip War, Time Has Become the Most Precious Resource
SEOUL — A quiet but consequential experiment is now underway at South Korea’s most influential company — and it could reshape not just the semiconductor industry, but the balance of labor, law, and corporate strategy in the country.
Samsung Electronics has become the first company in South Korea to receive government approval to implement a special extended work schedule of up to 64 hours per week for its semiconductor research and development (R&D) workforce. The approval, granted under newly revised labor regulations, marks a decisive shift in how Korea’s government and its corporate giants plan to compete in the global tech race — by stretching the workweek itself.
On its face, the move appears to be a procedural change. But for professionals watching South Korea’s critical semiconductor sector — a cornerstone of the global electronics supply chain — it’s a signal of far deeper transformations ahead.
The approval of extended work hours also comes at a moment of acute strategic pressure for Samsung, particularly in semiconductors. Despite aggressive investments, the company has fallen behind in high-bandwidth memory (HBM) technology, a cornerstone of the booming AI hardware market. Competitors like SK hynix have secured critical supply deals with Nvidia, while Samsung struggles to meet performance benchmarks, undermining its credibility with top-tier clients. Compounding the issue, Samsung’s foundry market share has dropped to 13%, compared to TSMC’s commanding 62%, exposing vulnerabilities in its logic chip capabilities. These shortfalls have already impacted profitability — operating profits declined nearly a third in late 2024 — and prompted internal restructuring, including leadership changes and a renewed “do-or-die” investment posture advocated by Chairman Lee. The labor policy shift toward longer R&D hours is thus not just a response to competition — it's a structural attempt to reverse momentum and rebuild technological leadership in AI-era semiconductors.
Global Foundry Market Share Comparison (Recent Quarters).
Foundry Company | Quarter | Market Share (%) | Source Note |
---|---|---|---|
TSMC | Q4 2024 | 67.1% / 67% | TrendForce reported 67.1%. Counterpoint Research reported 67%. Growth driven by AI and smartphone demand. |
Samsung | Q4 2024 | 8.1% | TrendForce data shows a decline from 9.1% in Q3 2024. Revenue declined due to lost orders not fully offset by new advanced-node customers. |
GlobalFoundries | Q4 2024 | 4.6% | TrendForce data. Revenue increased due to higher shipments despite slight price declines. |
A Legal Framework Rewritten: From Labor Protections to Productivity Imperatives
Just last month, South Korea amended its special extended labor regulation — previously limited to 3-month increments (renewable up to 12 months). Under the revised framework, companies can now apply for a 6-month extended period, with one renewal, during which designated workers may legally exceed the standard 52-hour workweek, reaching up to 64 hours per week in the first 3 months and 60 hours in the latter 3.
South Korea implemented a maximum 52-hour workweek law to curb the nation's traditionally long working hours. This legislation aimed to improve work-life balance, boost productivity, and address health concerns associated with overwork.
Samsung is the first to act under the new rules. Sixty-four R&D personnel in its semiconductor division are now officially authorized to work under this extended schedule, with mandatory health checks required every 6 months. Government officials have framed the move as a necessary adaptation to “accelerate development and maintain competitiveness in a sector where global timelines are shrinking.”
A government insider noted that “speed to innovation is no longer a luxury — it’s a survival metric in the semiconductor space.”
Inside the Pressure Cooker: R&D Workers at the New Frontier
For Samsung’s semiconductor engineers, this is not just a numbers game. It's a restructuring of the rhythm of daily life. The R&D cycle, already intense due to the nature of process development, now gains both the legal authority and corporate push to stretch further.
While some experts acknowledge that R&D work often requires focused sprints and non-linear schedules, others raise flags over the potential for chronic fatigue, mental burnout, and long-term health degradation.
One labor analyst emphasized, “We’re entering territory where the line between competitive urgency and institutionalized overwork begins to blur.”
The 64 hour per week trigger: Learning from China's 996 culture
Another emerging layer in Samsung’s calculus is its deliberate benchmarking of China’s high-intensity work culture, particularly in technology and manufacturing sectors. According to insiders familiar with internal discussions, Samsung’s leadership increasingly views China’s long-hours model — typified by rapid iteration, deep workforce mobilization, and a culture of extreme dedication — as a contributing factor to the efficiency and global ascent of firms like Huawei and BYD. Chairman Lee Jae-yong’s recent visit to China, where he engaged with companies operating under such regimes, appears to have reinforced this perspective. The move to approve up to 64-hour workweeks for Samsung’s semiconductor R&D staff is, in part, influenced by observations of how Chinese firms compress product cycles and accelerate development by leveraging longer working hours, specifically 996 culture. By emulating aspects of this model, Samsung is aiming to match China's execution speed without fully replicating its labor environment — a strategic adaptation that underscores the company’s belief that global competitiveness now hinges as much on organizational velocity as it does on technological capability.
The "996 culture" describes a controversial working hour system common in China's technology industry. It requires employees to work from 9 AM to 9 PM, 6 days a week.
During the China Development Forum in March 2025, Lee engaged with top Chinese leaders, including President Xi Jinping, and global CEOs from Apple, Qualcomm, SK Hynix, and BMW. His visit underscored Samsung’s dual-track strategy: while pushing for domestic R&D acceleration through extended work hours, the company is also strengthening international alliances to hedge against geopolitical uncertainties and secure its place in key markets like China, where Samsung’s sales surged over 50% year-on-year in 2024. Discussions with Xiaomi and BYD suggest Samsung is preparing to expand beyond traditional semiconductors into automotive electronics, a sector demanding rapid innovation cycles — reinforcing the company’s rationale for intensified R&D labor at home.
Labor Unions Push Back: “A Backdoor to Normalize Overwork”
Unsurprisingly, the backlash has been swift. Major labor unions, including the Korean Confederation of Trade Unions and the Federation of Korean Trade Unions, have condemned the move as a “loophole to legalize excessive labor”, arguing it undermines the core intent of South Korea’s 52-hour workweek cap — a law originally enacted to combat overwork, promote job sharing, and improve quality of life.
They argue that while the extended schedule requires employee consent and ministerial approval, the practical power dynamics within hierarchical companies make genuine consent difficult.
“It’s not just about how many hours people are allowed to work,” one labor policy researcher said. “It’s about the kind of work culture this legitimizes. Once a precedent is set at Samsung, others will follow.”
High-Risk, High-Reward: The Competitive Justification
From Samsung’s vantage point, the stakes are existential. With intensifying pressure from rivals such as TSMC and Intel, and a rising geopolitical tech war reshaping chip supply chains, time has become the most constrained variable in R&D strategy.
Internally, the company has reportedly assembled task forces focused on achieving breakthroughs in next-generation process nodes, including the highly anticipated 1-nanometer technology, with mass production targeted by 2029.
Semiconductor process nodes, like 1nm, label specific generations of chip manufacturing technology, historically related to transistor feature size. While the number is now more of a marketing term, smaller node names generally indicate denser, more advanced chips, reflecting the continued scaling predicted by Moore's Law.
The argument from management circles, though not made publicly, is straightforward: Without extraordinary R&D input, Samsung risks losing its edge in a sector where technology leadership translates directly into geopolitical relevance and market control.
The Industry Impact: Will Others Follow?
Insiders suggest that other semiconductor firms are now preparing to submit similar applications for extended work approvals. The Ministry of Employment and Labor has also pledged to streamline review processes and minimize administrative burdens for companies that meet the health and safety criteria.
In the words of one industry consultant, “Samsung isn’t just using the system — they’re shaping what the new normal could look like in Korean high-tech.”
Yet there’s significant uncertainty about long-term sustainability. SK Hynix, one of Samsung’s key competitors, has not pursued such extensions and continues to meet performance benchmarks under the existing 52-hour cap. This has raised questions about whether longer hours actually correlate with superior innovation — or whether they merely mask inefficiencies and create burnout risk.
Investors Weigh the Balance: Performance Boost or Liability?
For investors and market watchers, the Samsung decision introduces both short-term upside and strategic risk.
Upside:
- Accelerated R&D cycles could lead to earlier commercialization of advanced process nodes.
- Stronger positioning in key markets like AI chips, automotive semiconductors, and mobile SoCs.
- Clear government backing signals policy alignment with corporate goals.
Risk:
- Talent drain and employee disengagement due to overwork concerns.
- Potential social and political backlash if the model spreads across industries.
- Increased regulatory scrutiny, especially if worker health outcomes deteriorate.
An Asia-based institutional investor commented anonymously: “The market likes speed, but there’s a line where efficiency turns into exploitation. If Samsung crosses that line, the long-term valuation premium could evaporate.”
Health Protections or Symbolic Measures?
As a safeguard, the new system requires biannual health screenings for those under extended work conditions. However, critics argue that monitoring is not equivalent to prevention, and that institutionalizing long hours sends a mixed message about the government’s labor reform commitments.
Moreover, access to extended work premiums and official overtime pay, while technically a benefit, may not compensate for the erosion of work-life balance or the physical toll over time.
The Big Picture: An Inflection Point in Korea’s Labor-Corporate Compact
Samsung’s 64-hour approval is not an isolated HR event — it’s a referendum on how Korea balances its tech ambitions with its social contract. As the country bets big on high-tech supremacy, policymakers and business leaders are redrawing the line between productivity and protection.
What happens next could define a generation of labor norms in Asia’s fourth-largest economy.
The Price of Speed
Samsung’s new labor authorization opens a new chapter in Korea’s chip war strategy. The company may gain speed. But speed, in isolation, is not victory. The challenge now is not whether extended work can accelerate innovation — but whether the human system sustaining that innovation can endure the strain.
For investors, policymakers, and competitors alike, the next six months will offer the first glimpse of whether this high-intensity model can truly deliver — or whether it sets the stage for unintended fallout in Korea’s most critical industry.